Modern Slavery Statement
CED Stone Group
Modern Slavery Statement 2024
CED have produced this statement in line with and in
recognition of Section 54 of the UK Modern Slavery Act 2015. It describes and
links to our ethical strategy, targets, and current actions in relation to
prevention of Modern Slavery and forced labour, in our supply-chain. Forced
labour includes the range of activities such as recruiting, concealing,
transporting, or obtaining workers where a person uses force or physical
threats, psychological control, or other deceptive means to compel someone to
work.
CED make it clear to all our supply chain partners that any form of Modern Slavery, forced labour, debt bondage, child labour or any other act of forcing workers to do something against their will and where they have no choice, is totally unacceptable and will not be tolerated under any circumstance.
Other human rights abuses go “hand in hand” with Modern Slavery and our strategy is to monitor our supply-chain factories and watch for any warning signs or “red flags” that suggest there could be negative ethical trade impacts or human rights issues present. We include in this statement information on how we identify and prioritise human rights risks within our supply chain. We also report in this statement on our salient risks and strategy to mitigate these risks.
Natural Stone Industry background:
Natural stone production worldwide has some very complex supply chains. There can be some very good visibility at tier one factory level but much less, further down the chain at sub-contract and quarry level. Due to the sheer size, weight, awkwardness, and cost of moving raw natural stone quarry blocks, they are often processed into finished products at factories located beside the quarry source. In large countries such as China, this means that there can be a lot of production taking place at partner factories to the actual suppliers that importers are dealing directly with. Also, as with other industries there can be a substantial amount of sub-contract work done, as jobs are shared by neighbouring factories to manage lead-times. There are seasonal “highs and lows” in our market place and this can mean that there is a substantial amount of labour who are temporary and not employed directly by the factory. These temporary workers are often in a much more vulnerable position than the permanent workers; often transient, they are less likely to have formal contracts or insurance cover and are more at risk of suffering discrimination and labour rights abuses.
Often it is illegal and unchecked mines and quarries that can be responsible for bonding workers. Ultimately it will be the build-up of pressure on local and national Government bodies, to ensure enforcement of local and International Labour Organisation laws, that will bring about the necessary changes.
When you drill down into the whole concept and reasoning behind the Modern Slavery Act, it is to protect the workers that produce the goods that we consume here in the UK. When you buy something that costs very little it is probably the case that the workers who produced the product are being taken advantage of in some way. Low pay, long hours, physical and verbal abuse, forced and slave labour are much more likely. It is a conundrum which is hard to solve. We all look for a bargain but do not always consider the cost. In our industry when the contractors have the orders to place, their buyers have the job of finding the cheapest price. Our investment in Ethical work and the fact that we will only trade with ethically supportive factories, means that there is an extra overhead to be considered. The more pressure that the UK consumers place on business and Government to demand evidence of ethical sourcing the better. This is the best way forward for sustainable, across the industry change.
CED Ethical Supply Structure:
CED Stone Group always strives to lead by example in the way that we conduct ourselves and the fair way we interact and impact with our suppliers. We are conscious of the footprint that we leave and work hard to ensure that our purchasing and business practices have only positive effects on the workers in our supply-chain. Our buyers and estimators receive ethical training on business practices and procedures. Ethics are at the forefront of our commercial business decisions, to ensure good practice methods are adopted and minimum risk of harm for workers in our supply chain.
Company size is important when it comes to how much influence one can realistically exert on supplier factories. However, CED Stone do not see this as an excuse for any acceptance of Modern Slavery. We rigorously inspect and question supplier sites to look for signs that human rights abuses are, or might be present. Experience has taught us that collaboration and multiple stake-holder programmes, are the best way to influence improvements in regions, where our business levels, methods and reach alone, cannot affect any substantial positive ethical change.
CED overseas supply chain geographical spread:
It has been key that we fully map our supply-chain to ensure that we know where our stone comes from and where it is being worked, so that we can assess the conditions that workers producing our goods work under. Historically we have sourced the majority of our imports from factories in both China and India. Through research and mapping we identified these as our highest risk areas and have targeted most of our ethical resources there. However, major changes to stone sourcing market conditions, initially triggered by Covid 19, resulted in a major swing away from Asian factories. This has led to European stone supply being much more utilised since the latter half of 2021 and as you will see from the chart below, European factories continue to form the bulk of our imports. We also source stone products from the UK. but our ethical work is focused on over-seas supply. We do though, continue to be vigilant and monitor these operations too, so that we can ensure that there is no forced or slave labour present and that human rights are fully respected.
The Covid pandemic led to long periods of “lock downs” in 2021 and 2022. Some of the “knock on” effects from this led to shipping container rates from Asia rising dramatically in 2021. Average container rates soared by up to 20 times more than they had been previously.
During the course of 2024, container rates from the Far East are again proving quite volatile, with the global conflicts in particular pushing the prices upwards. We do not anticipate big swings back to Asia even if rates settle down again, as the whole bedrock of the industry has changed.
This considerable shift in Natural Stone supply chain sourcing, has led to many European factories being able to become more competitive than before with faster production and “lead in” times. The surge in business levels since 2021 has allowed a lot of the European factories to invest in developing in new areas, fixing new more efficient saws and upgrading other machinery and plant. Their efficiency levels and capabilities have increased considerably on the back of this. Additionally, the customer led market trends are dictating a preference for sourcing British and European stone products, in full consideration of improving ethical impact and decreasing carbon footprint.
The following chart shows our percentage of business by value for the different sourcing regions for the twelve-month period to October 30th 2024. Europe remains strong and still accounts for almost 70% of our imported purchases.
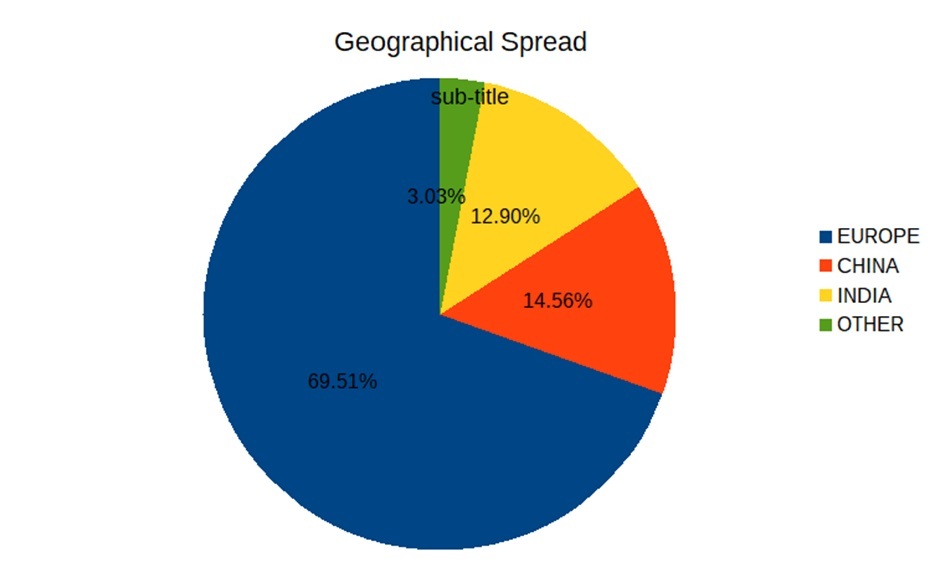
Our sourcing areas of greatest ethical risk however are still China and India, so they remain the focus for our ethical work. Indeed, the saliency risk levels for human rights abuses have increased in these countries on the back of “Covid lock-downs” and factories generally having fewer orders than before, meaning less overall work available for their workers. Our overall influence has diminished somewhat in these countries as we are less able to place steady, long-term forecast stock orders, which helped us considerably to promote discussions for action, change and improvements.
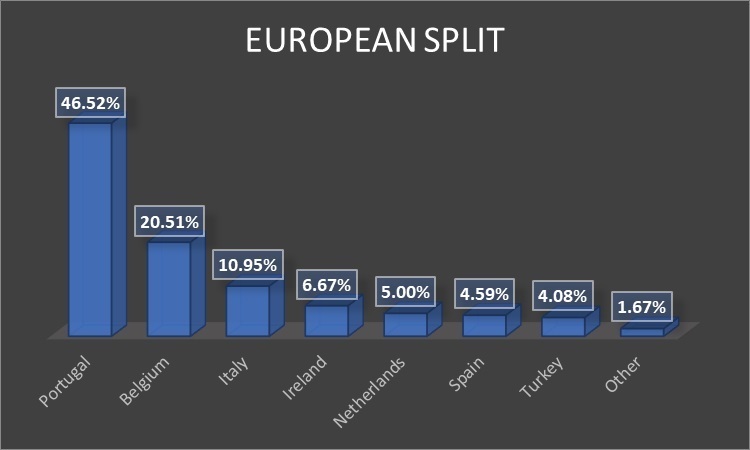
European Country supply breakdown 2024
This chart shows our
percentage split of imported European stone sourcing by Country.
The geographical spread of our imports is now settling into a consistent pattern, as can be seen from the below chart showing the last three years of data:
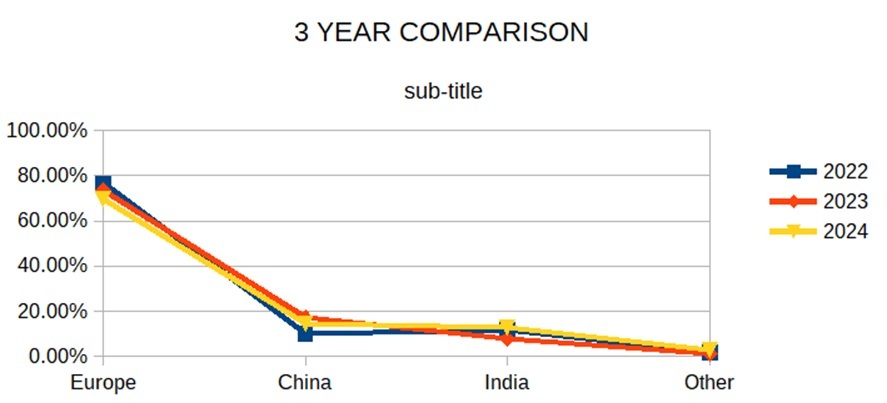
We now list all our supplier factory sites on the Open Supply site (link below):
ETI Membership:
The Ethical Trading Initiative (ETI) is a leading alliance of Commercial Companies, Trade Unions and NGOs, that promotes respect for worker’s rights around the globe. Their vision is a world where all workers are free from exploitation and discrimination, and enjoy conditions of freedom, security, and equity.
Global supply chains are highly complex and challenging for companies committed to eradicating Modern Slavery. Worker’s rights issues are often deep-rooted and widespread and are best tackled through collaborative action. Through our involvement with ETI we can harness the expertise, skills, and resources of their alliance members to identify these issues and help develop innovative, long-lasting solutions.
We have been full and active members of ETI for several years and have worked on collaborative projects such as the RSWG (Rajasthan Sandstone Working Group).
We believe that working with ETI and having our suppliers work to their Base Code of labour practices, is an essential for companies who are serious about Ethical Trade and eradicating Modern Slavery. The ETI Base Code is founded on the conventions of the ILO (International Labour Organisation) and is an internationally recognised code of labour practice:
1. Employment is freely chosen
2. Freedom of association
3. Working conditions are safe and hygienic
4. Child labour shall not be used
5. Living wages are paid
6. Working hours are not excessive
7. No discrimination is practised
8. Regular employment is provided
9. No harsh or inhumane treatment is allowed
The level of experience and knowledge that their tripartite of members bring and of which members have access to is vast and invaluable. They lead, guide, and monitor their members and ensure that you are always thinking forward and working to identify and resolve human rights issues and improve conditions for workers.
Supplier Participation:
Many of our key suppliers have been working together with us for twenty and thirty years plus. These long-term supplier relationships are crucial to ensure year on year improvements for the workers. Building long term, open and honest relations with our suppliers has allowed us to be well informed and work with them to instigate positive change. This has allowed us greater access to workers for interviews and training, allowing us to better understand their situation and priorities. It is crucial that suppliers are fully on board, with regards to treating the workers with respect and encouraging them to exercise their right to have the freedom, to choose where they work.
CED Business Ethical Process, Risk Assessment and Due Diligence:
Suppliers must sign up for and agree to abide by our Supplier Code of Ethical conduct. They must also sign our Ethical Business Contract. These documents highlight and focus on the principles laid out in the ETI Base Code
Supply Chain supplier sites must be fully mapped along with related quarry sources. Due diligence must be established for the relevant sector and an understanding of cultural and country-wide issues established. Using our knowledge gathered over years of purchasing natural stone, we initially manually risk assess based on known supply Country and region risks as well as other available information gathered. This information can be from multiple sources – internet research, supplier surveys and discussions, known industry risks, ETI, ILO, NGO and Commercial research surveys, reports and publications. Sites are graded by risk level based on this information using spreadsheet analysis and ISO 9001 risk assessment process and procedures.
There then follows a time-bound process of questionnaires, site inspections, audits, and continuous monitoring to ensure that no Modern Slavery or other Human Rights abuses are present in the tier one factories that make our finished products. As we run through these processes we can adjust risk priority level, as findings tell us in more detail about the level of risk for individual production sites.
Our general method for information gathering and initial breach targeting and resolving takes the following shape: Formalise CED policy with regards to Modern Slavery and Base Code principles. Ask ethical questions at time of first contact. Inspect site to look for any areas where issues might suggest a possibility of involuntary work or poor human rights practices. Discuss with factory management and get worker input. Conduct audit to establish any gaps in Base Code compliance, discuss gaps and work with supplier to resolve. Conduct worker interviews to hear their voice and understand their situation and priorities. We have not uncovered any Modern Slavery within our tier one supply chain. However, we remain vigilant and continue to implement small ethical “step by step” improvements to strengthen the worker’s position. These methods outline our business processes, built into our systems of supplier approval under our ISO 9001 quality procedures.
We help to encourage good practice at production sites which limits or eradicates the requirement for slave labour. Such as making sure the workers earn a living wage and all workers are given formal employment contracts.
Over time SMETA audits are necessary at most factories we regularly use when purchasing from our over-seas supply-chain. These audits are assessed against the ETI Base Code and local laws. We must stagger these audits over time, in a balanced and practical way and within Commercial limitations. CED and third-party inspections are very useful in the interim to establish where ethical and Human Rights issues may be present. With the changes to our supply sourcing structures (outlined above) and with many periodic factory and quarry closures in China this very much proves to be a “moving target” and requires regular review.
As the relationships with suppliers develop, we seek to go beyond audit and capacity build with our supplier. This currently includes investment in training, financing H&S gear, supplying ethical tools and systems guidance.
The ongoing sizeable reduction in orders to our identified higher risk countries China and India, has reduced our leverage with our trading partners in these countries. The reasons for these shifts in purchase countries are described in detail in the “overseas supply and geographical spread section” above. Therefore, we realise more than ever, the importance for us to find ways to collaborate with other stakeholders to increase our scope for achieving further positive influences on Human Rights issues for the workers in our supply chain. Our work in conjunction with ETI allows us to take part in collaborative projects where we can work to achieve joint impacts, increase our understanding of current country trends and legislation, as well as learn new methods from good practice by others. These joint projects include, reviewing framework for Responsible Purchasing Practices in manufacturing supply chains and tackling Human Rights saliency issues for Seafarers working within logistical supply chains.
Salient Labour Rights Issues:
Our focus remains in China and India as the two most “at risk” sourcing countries we buy our natural stone products from. This is where our research, using the above risk assessment methodology, has shown that salient labour rights issues are more likely to be present. We seek to identify the full range of human rights that could be negatively impacted by our activities and through our business relationships.
Potential issues (Shandong province, China) – Living wages are paid, no discrimination is practiced, regular employment is provided.
Two tier one factories that we deal with in North Shandong province, China, employ temporary migrant workers. We initially identified through audit that many of the temporary workers employed are farmers who travel to find work, out-with the harvest and planting seasons. Further detailed information has been gathered through questionnaires, supplier discussions and worker interviews.
The temporary workers do not receive the same employment contracts as the permanent workers. The temporary workers are paid piece rate (by how much they produce) and are not salaried like the permanent workers. This makes it harder to establish whether they are in fact earning a comparable living wage, when set against normal working hours. Recent “Covid lock-downs” and the overall slowing down of exports due to shipping costs and other market conditions have led to the factories being less busy and thus, less able to keep the temporary workers in regular work. In 2023 there has been an up-tick in business and the factories are busier again
We have prioritised these issues because historically we have strong links with these factories. In the past we have been able to place on-going, regular, stock orders and this has helped us to gain access directly to the workers. Our ethical effort includes supplying free H&S gear to the factories to distribute to both seasonal and permanent workers. Worker H&S training. Worker interviews to better understand the priority issues they face. We continue trying to find an NGO or TU to work with in collaboration in the region. Regular factory discussions. Recent Covid restrictions and reduction in purchases have slowed down some of our work but we continue to keep a focus here. Our intention is to conduct some further training and worker interviews in Spring 2025 to establish the workers current situation and evaluate any changes so we can update our strategy moving forward.
Potential issues (Rajasthan sandstone quarries) - No discrimination is practiced, no harsh or inhumane treatment, no child labour, working conditions are safe and hygienic.
The Rajasthan natural stone industry employs over 3 million people. There are 150,000 plus quarries many of which are small-scale, informal operations. Labour risks are mainly concentrated at quarry level due to how labour intensive the work is, the remoteness of the quarry locations and the lack of regulations in place.
We have done a lot of positive ethical work, with partner tier one factories in Rajasthan, which began with our involvement in the RSWG (Rajasthan Sandstone Working Group), which ran from 2012 through to 2018. This was a collaboration project with other commercial companies, ETI, NGO'S and other stakeholders. However, as established at that time and through discussions with NGOs and ETI as well as many published articles, there are a lot of Human Rights concerns at many of the sandstone quarries in the region:
- 150,000 plus quarries in the region many of which are illegal and unregistered.
- Early mortality rate in region.
- Quarries located in inhospitable climactic areas. Extreme high temperatures.
- Many of the workers are migrant workers.
- Lack of fresh water and toilet facilities.
- Very dusty conditions.
- No other significant industry in region.
- Poor quality of education in region.
- Poor visibility within our supply chain.
Reasons for prioritising focus here:
- This area is known to be high risk.
- The average age of death amongst male workers at the quarries is 35. This can lead to children being forced to replace their fathers at quarries to pay off their debt.
- Increased vulnerability to exploitation and abuse.
- High mortality levels from silicosis which manifests itself in prolonged illness and painful death.
- Poverty and the lack of a social security network
- Our work in the region as a collaboration with the RSWG gives us better knowledge, influence and understanding.
- Children being cheaply available, hence have an easy access to work
- Lack of trade union activity in region
We discuss with and ensure our sandstone supplier factories in India only source block from legal, registered quarries. We insist that they inspect their stone sources and ascertain basic human rights are in place. It is imperative that they establish there is no forced, child or bonded labour present. We establish that they will only deal with quarries which use wet drilling equipment to reduce dust in the environment. Of course, we appreciate that we are comparatively, a very small importer, with limited influence in the region. However, through our involvement in work with the RSWG and the whole positive influence from that collaboration, as well as our on-going checks and supplier directives, we have helped raise awareness and increased pressure for action. Adding to the much more significant, excellent work efforts made by some of the NGOs in the region. Due to these and other factors, there have been improvements in the quarrying industry over recent years. The Government have become much more active and many of the illegal mines have been shut down. They are stricter now with making sure quarry owners comply with the legislation. Our recent information from suppliers and NGO's reports other positive changes at some of the quarries. We are not sourcing a lot of stone direct from India these days but the main tier one trading partner factory, that we work with have opened their own sandstone mines with their own employed workers. This means their own workers not only process, but will also quarry the stone giving a much greater control of H&S conditions, wages, site conditions and monitoring all aspects of HR issues. This means control and visibility from quarrying blocks to sawing and finishing the slabs. This cuts out the risk of block being sourced from inadequate quarrying operations.
Potential issues (Gwalior Factory, Madhya Pradesh, India) - No discrimination is practised, working conditions are safe and hygienic, living wages are paid, working hours are not excessive: as well as permanent workers this factory engages seasonal / contract workers.
This is still a relatively new Indian production site for CED, that we began dealing with in 2019. They fit in with our ethos for ethical values and are a family run business engaged in quarrying, manufacturing and processing of natural sandstone products sourced mainly in Kota, Rajasthan. The factory employs 75 permanent workers but also quite a number of temporary workers during busier seasons.
Our general observations of this factory are good and it is clear that the workers are for the most part, happy in their roles, treated fairly and motivated to perform well. Also, they have a route to discuss directly with management if they have issues that they need to have resolved. However, led by ETI as part of our Fair Purchasing Practices project, fifty workers were interviewed to establish where salient risks may be lurking and where improvements could be induced. This led to the following areas for action:
Many of the workers do not have formal contracts.
Female workers in the minority.
No union presence and lack of official Grievance procedure / committee.
Some workers potentially working beyond legal overtime hours.
Lack of formal H&S training.
Temporary workers do not have ESI and EPF insurance.
Following on from the success of the multi stake-holder collaboration in Rajasthan (2012 to 2018) and working in conjunction with our long-term Indian supplier, NNG Group, we have seen many significant ethical improvements at their tier one factory levels in India. We found these potential salient issues present, based around discrimination of contract workers, no recording of contract worker hours, lack of safety gear distribution and uptake as well as poor HR documentation such as employment contracts and payment records. Some of the “step by step” improvements now in place, include new shaded garden areas for breaks and meal times. Safer working areas with more safety gear distribution to both permanent and contract workers. New HR systems including employment contracts and payments direct to bank accounts. H&S meetings and training. Worker grievance committee. Contract workers hours now recorded. This further increases the ethical transparency of our Indian production.
This work has increased our awareness that seasonal / contract workers can find themselves disadvantaged when compared to permanent workers. Different payment methods, less allowed use of H&S gear and unrecorded payments are issues that we have come across before. So, we are using the lessons learned and methods and tools used to help avoid these discriminations taking place at this newer supplier factory.
Along with the factory management we are working on an improvement plan to close some of these gaps and improve the situation for the workers:
Setting up health check-up camps.
Introducing formal H&S training.
Employing one key person with h=whom workers can share concerns and issues.
Contracts for all permanent and temporary workers.
Improve our long-term forecasting to try and alleviate peaks and troughs in production.
Ensure we pay the factory within our agreed payment terms.
Our plan is to have a follow-up visit to the factory early next year to check on progress against these targets. CED have also offered to arrange some training in conjunction with the SFNS (Sustainability Forum on Natural Stones). The factory can call on this if they need assistance.
Potential issues (Jinan factory, China) - No discrimination is practiced, living wages are paid, working conditions are safe and hygienic.
This factory does not pay much funds for the social insurances for their seasonal workers. We have prioritised this because these seasonal workers are in a vulnerable position if they are unable to work due to sickness or accident and cannot, or do not want to, pay for these insurances themselves. There is a danger that they would not get paid while unable to work and would have no avenue to claim any benefits. They are often also the “bread winner” for their family.
China's Social Security System consists of 5 mandatory insurance schemes (pension fund, medical insurance, industrial injury insurance, unemployment insurance, and maternity insurance).
Pension Insurance:
Pension insurance ensures that employees in China will have money available to them after retirement. Money is accumulated in the employee’s individual fund. Normally, employees must make 15 years’ worth of contributions in order to receive a pension in China. Employers also contribute to these funds.
.
Medical Insurance:
Medical insurance covers a portion of the cost to treat Chinese workers’ illnesses or other non-work-related injuries. The employer and employee must pay into this form of social insurance on a monthly basis.
Industrial Injury Insurance:
This pays for treatment stemming from a work-related injury or illness. Only Chinese employers make monthly contributions to this type of social insurance; employees do not.
.
Unemployment Insurance:
Unemployment insurance provides monetary benefits to unemployed workers for up to 24 months. In most cases, only employers contribute to this form of social insurance. However, employees in certain areas may also be required to make monthly contributions to this fund.
Maternity Insurance:
In China, many pregnant women receive paid maternity leave. Employers, but not employees, are required to make monthly contributions for this form of social insurance.
Factory managers want to be as competitive as possible and paying out insurance contributions for temporary workers is often seen as an unnecessary overhead. When workers are only working for short periods of time, they want to maximise the amount of money they earn and take home. Often, therefore, the workers do not want to contribute to such things as pension funds or medical insurance. So, the problem is multifaceted and quite complex.
Again, we have distributed free H&S gear to these factories and ensured that they share with the seasonal workers. We have also provided some H&S training. Due to less orders our influence is reduced right now but we continue to question the factory management about this issue. We continue to try and find NGO partner in the region to assist with getting the factory to change their stance and help with worker education. Recent Covid restrictions and reduction in purchases have slowed down some of our work, but we continue to keep a focus here and plan to visit the factory again now that restrictions have been lifted and once business levels dictate. We continue to further raise awareness with workers on their rights and the importance of having these insurances in place.
Potential issues (Portuguese factories) - Working hours are not excessive, no discrimination is practised, regular employment is provided:
We have prioritised this situation because the bulk of our imports are now made from Portuguese factories and our influence is quite strong.
When we have audited our European trading partners in the past, any non-compliance has been very minor and quickly resolved. However, factories in Europe had received unprecedented levels of orders in 2022, due mainly, to rising shipping costs and container shortages when sourcing stone from China. They had mostly over-committed their production facilities and were behind with orders. Considerations here include excessive overtime to increase production output, busier factories increasing H&S dangers, new staff to help with the extra work need proper training, when the “bubble bursts” how secure is the employment for the new workers.
In September 2022 we interviewed the factory managers at the Verona stone show to understand their current position and to find out their thoughts on overtime and workers safety. We also followed up with questions to formalise their position and set some objectives. In 2023 some of the UK stone industry companies moved their stock ordering back to Asia lessening the European demand somewhat. However, these European factories remain much busier than pre-2022.
We sent a delegation to Portugal in the Spring of 2024 to dig deeper into the current situation at our main Portuguese supplier factories and to check progress against our objectives. The factories we visited have all invested heavily in new saws and machinery since the boom of increased orders. Multi wire saws have been fitted which are much more accurate and are much more efficient, speeding up production and lessening waste. Overtime is not required and they operate with a much-improved carbon footprint. Skilled workers are in short supply in Portugal and to employ, and keep these workers, factories have had to increase wages substantially and improve working conditions. If they did not do this, then these workers will move on to another factory who will. We also noted an increase in female workers in quality assurance and supervisor roles.
Potential issues (Container ships) - Working hours are not excessive, no discrimination is practiced, employment is freely chosen, freedom of association, working conditions are safe and hygienic.
The Seafarers crises in May 2020 brought to light the Human Rights abuses and challenges faced by workers in the logistics sector that moves goods and produce around the world. 80% of all goods imported into the United Kingdom arrive via sea freight. Despite transport and logistics being necessary in almost every product supply chain, it remains an HRDD (Human Rights Due Diligence) blind spot.
Instigated by the seafarer crisis and the collaboration between ETI and their members and the ITF (International Workers Transport Federation). We have started looking in more detail, at some of the less visible parts of our supply chain. Beginning with conditions and human rights for workers on the container ships that transport our stone. We have prioritised this because of the inhumane treatment of seafarers during Covid, which was impossible to ignore. The collaboration between ETI and ITF, making expert information available and immediate pathways to lessen our negative Human Rights impacts. As well as seeing this as a great opportunity to get more visibility of hidden areas.
During the height of Covid, many sailors were unable to come ashore because crew change ground to a halt. Some sailors started refusing to work and blank sailings occurred. Also, equipment shortages and price rises, for cargo movement, were increasing at an unprecedented rate. Shipping owners and investors exploited this opportunity to increase profit while sailors were fighting daily fatigue. International maritime labour conventions were being flouted, and crews feared that they would be blacklisted for future work if they refused to agree to demands. None of these extra profits were passes down to the working sailors.
ITF holds a Global Collective Bargaining Agreement (CBA) for seafarers. Seafarers working on vessels covered by this agreement are guaranteed protections around working time, leave, compensation for disability, maternity pay and grievance mechanisms. An ITF agreement guarantees Trade Union consultation, negotiation, ongoing engagement, and monitoring in both implementation and grievances essential for HRDD compliance. ITF assisted with a Maritime Human Rights Due Diligence Health Check on vessels carrying our shipments from January 2020 through to October 2021. It transpired that 81% were covered and had ITF approved CBA in place. The good news was that this meant that the seafarers on 81% of the vessels we used, had access to protections and recourse through these agreements. Of course, this also meant that 19% of the vessels bringing containers from Asia in 2021 had no CBA in place. This was unacceptable and we have since been working to improve with a final target that all our vessels, without exception, will have a CBA in place no later than 2025. We have since been actioning systems with more demands on our Freight Forwarders, to improve this situation. In 2022 where possible, we started turning down vessels that were not covered and also managed to alert ITF to these vessels that were not covered and they were sometimes able to get a CBA for that vessel in place on the back of this. During the year we were also given access to an ITF tool where we could check status of vessels ourselves. We also instructed our Forwarders to commit to offering only vessels with an ITF agreement on board or national flag vessels with a national CBA in place. During that year we found that the faster and more competitively priced vessels that we were offered tended to be uncovered and flying flags of convenience (FOC), of countries with minimal HR regulations. Our research suggests that as the Shipping industry was still in flux with thousands of containers misplaced, there was still an opportunity for suppliers of shipping services to maximise profits by blanking vessels and using lack of suitable agreements to push forward vessels with no protection for Seamen in place. In a competitive shipping market FOC’s offer shippers the opportunity to run their vessels on the cheap with lower fees and minimal regulations. In reality during this period there was often almost no option but to use uncovered vessels and this mixed with our vast reduction in imports from Asia led to a very similar outcome to the previous Health Check period. Moving in to 2023 and 2024 we have almost exclusively used a Freight Forwarder who works with us and uses the ITF provided tools to check for coverage before offering us the vessels. This has been working well and is shown in the results of our latest Health Check conducted on our vessels used by ITF. We are pleased to confirm that only 1 of the vessels that we had containers on board dis not have an ITF approved CBA agreement and 1 other vessel did not have an acceptable CBA agreement. This means that now the percentage of vessels covered by agreements is in the high 90 percents which shows excellent improvement. We will continue with annual health checks to ensure that we are continuing to have the Sea farers working on the ships bringing our stone to the UK protected by CBA agreements.
During 2023 on board vessels used by CED Stone Group there were three cases of owed wages, including wages not updated including wages not updated for the New Year’s CBA and crews not receiving the correct wages for their work. With the support of ITF inspectors, backpay was obtained.
Also, there were two instances of crew needing assistance with repatriation, including one seafarer who required medical treatment. After the intervention of ITF Inspectors these crewmen were allowed to go home.
With the presence of live ITF approved and/or ITF acceptable CBA’s, ITF inspectors have the right to access the vessel. ITF agreements protect seafarers even when issues arise, by ensuring access for Union representatives such as ITF Inspectors, thus demonstrating that goods should only be shipped on vessels covered by an ITF CBA.
ITF also has a Warehouse Charter which covers multiple warehouses worldwide. In the first instance we are seeking to establish if sites that our goods pass through are covered by their Charter. We are still in the process of the necessary mapping the warehouses that our goods are delivered to before getting to the ports and loading in containers. These are third party sites, neither controlled by us or our suppliers where visibility of HR conditions and agreements for workers is low.
FOA (Freedom of association) and collective bargaining:
We are very familiar with United Nations Guiding Principles in this area and we are fully supportive of the ETI (Ethical Trading Initiative) Base Code clause on Freedom of association – summarised as follows:
- Workers, without distinction, have the right to join or form trade unions of their own choosing and to bargain collectively.
- The employer adopts an open attitude towards the activities of trade unions and their organisational activities.
- Worker’s representatives are not discriminated against and have access to carry out their representative functions in the workplace.
- Where the right to freedom of association and collective bargaining is restricted under law, the employer facilitates, and does not hinder, the development of parallel means for independent and free association and bargaining.
Over the years we have built up our knowledge and seen first-hand, how Trade Unions and Worker Committees can increase the likelihood of workers succeeding in negotiating better terms and conditions of employment. We stress to our supplier management, the importance of allowing workers to negotiate and have a “voice” in this way.
At our primary Indian supplier factory in Bundi, India, we facilitated a training course on operational grievance mechanisms in the work place. This included step by step guidance on establishing rules and procedures for the setting up of a grievance committee at the factory. They then created a position and appointed a dedicated person on site to run and attend the worker formed committee meetings. They now have a regime of scheduled meetings on H&S and grievance structured on the learning from the training session.
There are no active Union representatives in most of the areas of China that we operate. We share good practice on grievance mechanisms with tier one factories and discuss with management during visits the need to have open dialogue with workers. We also discuss this labour right in talks with workers when we gain access. Also, in China, we arrange for our tier one supplier/ partner to share information on workers’ rights, with Workers during interviews.
In our European supply chain, most of the workers either have access to unions or are union members and robust grievance mechanisms are normally in place. Our supply base has changed considerably over the last two years and a greater proportion of our goods are sourced from Europe. This means that overall, our supply base has gravitated to more robust systems.
We are aware from audits and interviews that most of our workers have some sort of avenue to air their grievances, although sometimes not as official as we would want. One of our ongoing targets is to improve the formality and visibility of grievance process in our supply-chain moving forward.
We appreciate the need for workers’ rights and protections to extend to all tiers of our supply chain. Where there is no active Union available, it is important to establish the best form of independent worker committee. An example of this is our policy to ensure that container goods are shipped on vessels covered by International Trade Federation agreements.
We comply with both National laws and international instruments and standards on freedom of association and collective bargaining.
We reinforce with our suppliers that workers of all status – whether permanent, temporary, contract or seasonal – must have access to fundamental workplace rights and protections. There should be no discrimination regarding who can join Unions or worker committees. Collective agreements should apply to all regardless of status.
Covid19:
The last years have presented unprecedented issues with the global virus pandemic. This has limited our ability to travel, audit and run training courses. However, we have been required to be extra careful, to ensure that the workers are safe and have the necessary protections to survive. Also, that their employment is secure and that they have enough money to get them through the periods of Lock-down.
- More engagement with suppliers to reinforce the H&S messages passed down by the WHO (World Health Organisation); regular hand washing, wearing face masks, social distancing and having hand sanitiser available for use.
- Fulfil our payment obligations promptly for ongoing work to keep their cash-flow fluid. Beyond this insist that they must pay workers for the work they have done on our orders even if running behind.
- Pay for orders in progress even if they cannot be finished or shipped.
- Where possible consider early payment so that workers can pay for medication and food and survive periods of isolation.
- Accept order delays without passing on any associated costs.
- Avoid cancelling orders due to late production.
- Engage with our suppliers to ensure that workers are not being asked to work excessive overtime when factories reopen and orders are delayed.
- Ensure suppliers accept that workers may feel unsafe if they return to work and try to ensure that they are not disadvantaged for deciding to stay away.
Covid lock-downs in Shandong China can lead to migrant and seasonal workers in stone factories being unable to work and earn money. The factories do not have emergency plans to fund these workers and there are not always the correct insurance covers in place. This leads to saliency issues which could include children having to work to earn money for basic food and lodgings where their parents are no longer earning wages. We are keeping very close vigilance on these potential situations.
CED Business Ethical Principles:
Responsible business conduct and respect for human rights are at the heart of our operations.
When identifying future business opportunities, we do so in partnership with others that are equally committed to respecting labour standards and advancing human rights.
We strive for greater visibility and transparency within our company and communicate externally about the value of corporate responsibility.
We offer sustainable work to our suppliers and encourage economic growth. Ensuring equal wages with no discrimination.
Child labour and Modern Slavery are completely unacceptable and we will strive to eradicate these practices at every juncture.
We champion labour rights and promote a safe working environment.
Ethical Communication:
At all times we strive to keep ethical trade and the Ethical
Base Code principles at the forefront of our business strategy. The more visible
and vocal we are about Modern Slavery will encourage others to support our
stance and prioritise systems to avoid.
We keep the topic of Modern Slavery visible in meetings and on social media.
We systematically remind suppliers of their responsibilities to the workers they employ.
We regularly discuss the topic with suppliers and encourage them to think more about how they can improve the environment and situation for their workers.
Current work and strategy:
Worker’s priority is key to how we are developing our strategy and ensuring Modern Slavery is not present in our supply chain. We have gained much better access to workers over the last few years: workshops in India where priority worker issues have been discussed and actioned; CED staff talking directly to workers in India and China; tier one supplier organised worker discussions with factory workers at the factories they use for our orders. SMETA audits which include worker interviews. Surveys which include worker comments such as the Independent Evaluation of ETI Sandstone Programme in Rajasthan.
Working with ETI and other stakeholders on collaborative projects to increase our influence over mitigating salient Ethical Human Rights issues in our supply chain
We will continue to develop ways of understanding workers situation and concerns and adapt our process and strategy accordingly. Whilst we focus our resources in Asia, we also audit factories in Spain and Portugal to ensure there is no forced labour in place there. This forms part of our Iberian complete compliance programme. Beyond this we are vigilant here in the UK with regards to dealing with companies and people who provide services for us, such as maintenance and cleaning.
Current Targets to increase the effectiveness of our strategy to tackling Modern Slavery:
● Ensure our guidance regarding Covid19 related issues are fully complied with by the factory management.
● Find other means to monitor and mediate while travel restrictions are in place.
● Further Chinese factory worker interviews to monitor their situation.
● Continue to assimilate Fair Purchasing Practices into our systems and procedures.
● Increase our activities of working with our trading partners to help them ensure that there are no contracted employees on their sites who are forced to work against their will.
● Review our inspection and audit programmes to monitor if they are effective and calculating what else we can do to support our “zero tolerance” approach to Modern Slavery.
● Ensure our supplier contracts fully cover our criteria and demands with regards to employment of workers.
● Ask how we can be more effective in collaborating with both customers and suppliers to support our approach to protecting human rights in our supply chain.
● Increase transparency and visibility further down through our supply-chain.
● Take further, active involvement in collaborative ethical partnerships with other stakeholders in the areas our goods are produced. This is mainly by working together with ETI, Trade Unions, NGO’s and other Commercials on current programmes and projects.
Calum Fraser – Director Commercial

(Approved by CED Board of Directors)